Maximizing Efficiency with Advanced Ship Loading Technology
Maximizing Efficiency with Advanced Ship Loading Technology
Blog Article
The Future of Automated Ship Loading Systems
Selecting the most appropriate ship filling process is an essential part of ensuring ship loading systems interface procedures, charge management, and the secure managing of materials. With various options available, choosing the one which aligns together with your specific needs can appear overwhelming. That information may go you through essential factors to take into account prior to making your decision.
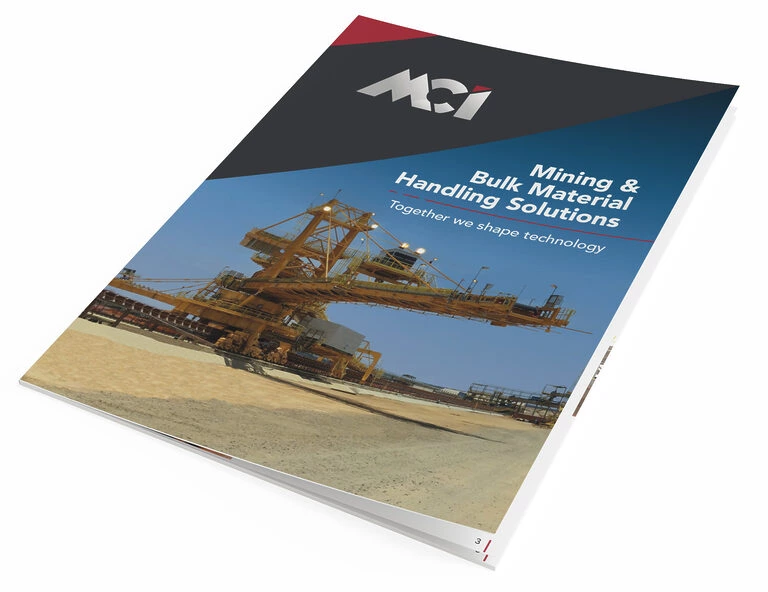
Understand Your Material Handing Needs
The type of substance being handled profoundly impacts the option of vessel filling equipment. For instance:
Dried bulk products (like feed or cement) may possibly involve surrounded conveyor strip programs to reduce wastage and environmental impact.
Wet or sweaty components, such as for instance slurry, demand particular handling techniques to prevent clogging.
Hazardous materials require techniques with additional security and containment features to comply with regulatory standards.
Before generally making a choice, classify your materials and determine their physical houses, such as for example particle size, water material, and flowability.
Examine Capacity and Throughput
Every ship launching operation is exclusive in their degree and demand. Establish your throughput necessity in loads each hour to gauge the system's capacity. Something that fits (or somewhat surpasses) your capacity needs ensures maximum operations without overburdening equipment.
For high-capacity wants, long-term performance generally exceeds higher preliminary costs. For smaller masses, a more compact and economical process may suffice. Assure the system can handle top working situations without reducing their performance.
Prioritize Environmental Considerations
Environmental sustainability has become more critical in vessel running operations. Many techniques today come equipped with features that reduce dirt, sound, and emissions. Look for:
Dirt get a grip on methods to stop material reduction and reduce health threats for operators.
Energy-efficient patterns to reduce working charges and carbon footprints.
For regions with rigid environmental regulations, prioritizing sustainability may avoid fines and improve your company's reputation.
Focus on Freedom and Customization
Slots usually handle varied products or vessels of varying sizes. A variable vessel packing program that could adjust to adjusting demands is a clever investment. Look for techniques with:
Flexible designs (e.g., extendable conveyors or variable growth lengths) for increased versatility.
Modular parts to modify and upgrade the device as needed.
Such characteristics increase long-term electricity and reduce steadily the likelihood of seeking an entire process change in the future.
Contemplate Ease of Maintenance
Downtime may be expensive. Go for programs designed with ease of preservation in mind. Characteristics like quick-access factors, simply replaceable parts, and contemporary diagnostics instruments reduce restoration times and help recognize possible problems before they occur. Protective maintenance programs also can prolong the system's lifespan and maintain efficiency.
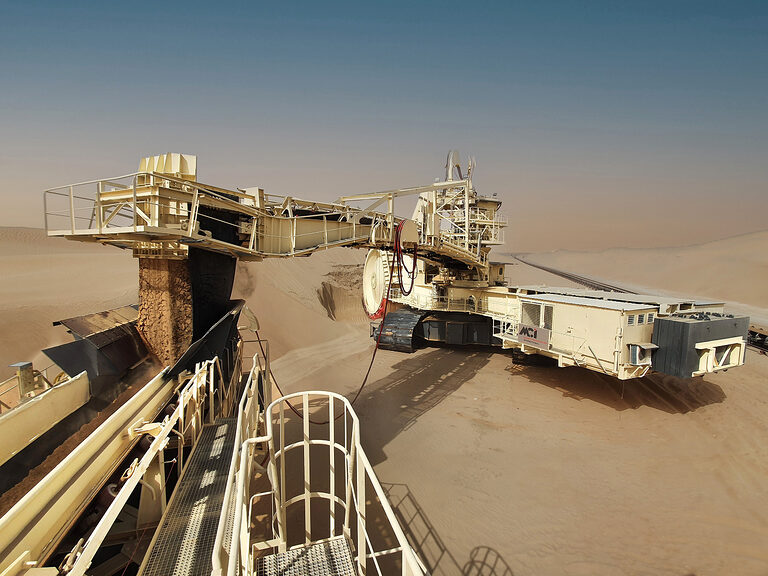
Think Forward About Automation
Automation is quickly transforming the transport and logistics industry. Contemporary ship running techniques frequently contain automated controls for greater detail, paid off individual mistake, and increased safety. While it might involve a greater transparent charge, automation usually decreases long-term work expenses and enhances detailed reliability.
Ultimate Feelings
Choosing a vessel launching system is not more or less the equipment's complex specs. It's about aiming the device together with your operational needs, environmental requirements, and future scalability. By knowledge your needs and prioritizing essential functions, you'll buy program that supports your operations for years to come. Report this page